
Kronos Fusion Energy Incorporated is at the forefront of developing advanced aneutronic fusion technology, aiming to achieve a fusion energy gain factor (Q) of 40. Our mission is to provide clean, limitless energy solutions for industrial, urban, and remote applications.
Revolutionizing Prototyping and Production: A Case Study on Kronos S.M.A.R.T.'s Material Innovations
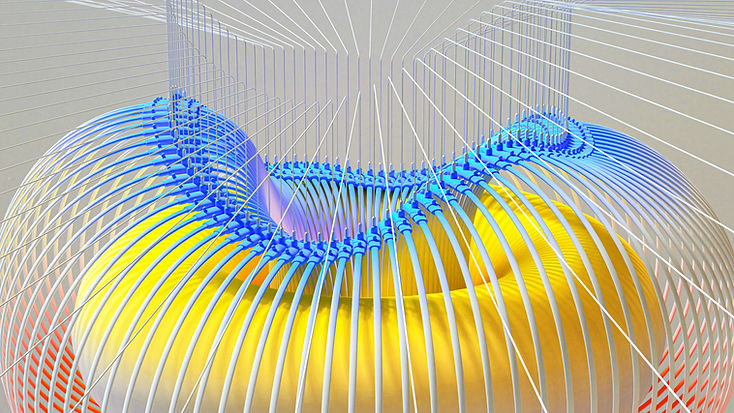
Introduction
In the rapidly evolving field of fusion energy, material innovations play a critical role in advancing technology. Kronos S.M.A.R.T. (Superconducting Minimum-Aspect-Ratio Torus) has been a frontrunner in this regard, implementing additive manufacturing and nanotechnology to reshape the prototyping and production processes. This case study examines how these innovations have revolutionized the approach to creating complex components and significantly reduced both costs and time-to-market.
Material Innovations in Kronos S.M.A.R.T.
1. Additive Manufacturing
Additive manufacturing, often referred to as 3D printing, is a process where material is added layer by layer to form a three-dimensional object from a digital model. In the context of Kronos S.M.A.R.T., this method has brought several benefits:
Rapid Prototyping: Accelerating the design and testing phases by quickly turning digital models into physical prototypes.
Design Flexibility: Enabling intricate and custom designs that would be challenging to create with traditional manufacturing methods.
Waste Reduction: Utilizing material efficiently, thus reducing costs and environmental impact.
2. Nanotechnology
Nanotechnology involves manipulating materials on an atomic or molecular scale. It has been pivotal in Kronos S.M.A.R.T. for:
Material Enhancement: Improving properties such as strength, durability, and conductivity, allowing for more efficient designs.
Precision Engineering: Creating highly detailed and precise components necessary for the advanced functionality of the system.
Revolutionizing Prototyping
Speed and Agility: Additive manufacturing has slashed prototyping times, allowing for more iterations and refinements in the design phase.
Complexity and Customization: With the ability to print intricate designs, engineers can explore innovative solutions without constraints imposed by traditional manufacturing methods.
Transforming Production
Cost-Efficient Manufacturing: Both additive manufacturing and nanotechnology contribute to reducing production costs through efficient material use and reduced waste.
Scalability: These technologies allow for small-batch production and easy scaling to larger quantities, providing flexibility in response to market demands.
Quality and Consistency: Precision offered by additive manufacturing and nanotechnology ensures that every part produced meets exact specifications, maintaining high quality across batches.
Real-World Implications
Energy Sector Innovation: Faster prototyping and efficient production align with the goals of sustainable energy solutions, making fusion energy more accessible and affordable.
Cross-Industry Impact: The methodologies applied in Kronos S.M.A.R.T. have potential applications across various industries, including automotive, aerospace, healthcare, and consumer electronics.
Conclusion
Kronos S.M.A.R.T.'s adoption of additive manufacturing and nanotechnology has proven to be a game-changer in the prototyping and production landscape. By allowing for rapid, flexible, and cost-effective creation of complex components, these innovations have positioned Kronos S.M.A.R.T. as a leader in fusion energy technology.
The wider implications of these advancements reach beyond the energy sector, promising to reshape the future of manufacturing across diverse industries. By continuing to explore and expand upon these innovations, Kronos S.M.A.R.T. stands as a beacon of technological progress with the potential to drive a new era of sustainable and innovative development.